Fisher snow plows are reliable tools for winter maintenance, but occasional issues arise. This guide provides expert tips to diagnose and resolve common problems efficiently, ensuring optimal performance.
1.1 Importance of Regular Maintenance
Regular maintenance is crucial for ensuring the optimal performance and longevity of your Fisher snow plow. Neglecting routine checks can lead to unexpected breakdowns, reducing efficiency and increasing repair costs. By inspecting hydraulic lines, fluid levels, and electrical connections, you can identify and address potential issues before they escalate. Proper maintenance also enhances safety, as malfunctioning components can pose risks during operation. A well-maintained plow ensures smooth functionality, reducing downtime and allowing you to handle snow-clearing tasks effectively. Schedule periodic inspections and adhere to the manufacturer’s guidelines to keep your Fisher snow plow in top condition throughout the winter season.
1.2 Common Issues Overview
Fisher snow plows, while durable, can experience common issues that hinder their performance. One prevalent problem is the blinking red light on the control panel, often indicating system errors or communication faults. Unresponsive buttons or controls are another issue, which may stem from wiring problems or faulty sensors. Hydraulic system malfunctions, such as clogged lines or low fluid levels, can cause the plow to function improperly. The lift mechanism may fail to raise or lower the blade correctly, and unexpected drops can occur due to faulty actuators. Blade angle adjustments might not work as intended, complicating snow-clearing tasks. Electrical issues, like blown fuses or damaged wiring, can disrupt operation altogether. Understanding these common problems helps in addressing them promptly, ensuring efficient snow removal and minimizing downtime.
Common Issues with the Control Panel
The control panel may experience issues like a blinking red light, indicating system errors, or unresponsive buttons, often caused by wiring problems or faulty sensors.
2.1 Blinking Red Light on the Control Panel
A blinking red light on the Fisher snow plow control panel typically signals a system error. Possible causes include a faulty sensor, low hydraulic fluid levels, or electrical issues. To diagnose, check the hydraulic fluid levels first, as low levels can trigger warnings. If the fluid is adequate, inspect the sensors and wiring for damage or corrosion. Consult the operator’s manual for specific error codes. In some cases, a controller swap with another unit can help identify if the issue is with the panel itself. If problems persist, contact Fisher Engineering support for professional assistance to resolve the issue and restore functionality.
2.2 Unresponsive Buttons or Controls
Unresponsive buttons or controls on the Fisher snow plow control panel can disrupt operation. First, ensure the controller is properly connected to the vehicle’s electrical system. Check for loose or corroded connections, as these can prevent signals from being transmitted. Inspect the wiring harness for damage or wear, especially near areas exposed to harsh weather conditions. If issues persist, try resetting the control panel by turning the vehicle off, waiting a few minutes, and then restarting. If the problem remains, it may indicate a faulty controller or internal electrical malfunction. In such cases, contact Fisher Engineering or a certified technician for further diagnosis and repair to restore functionality.
Hydraulic System Malfunctions
Hydraulic system issues can cause plow malfunction. Common problems include clogged lines, low fluid levels, or faulty valves. Symptoms may include slow or jerky movements. Always check fluid levels and inspect lines for blockages before operation. Refer to the troubleshooting section for detailed solutions to restore hydraulic functionality efficiently.
3.1 Clogged Hydraulic Lines
Clogged hydraulic lines are a common issue in Fisher snow plows, often causing reduced performance or complete system failure. Debris, dirt, or freezing temperatures can block the lines, disrupting fluid flow. Symptoms include slow or erratic plow movement, inability to lift or angle the blade, and unusual noises during operation. To diagnose, inspect the hydraulic lines for visible blockages or kinks. Flush the system with clean hydraulic fluid if contamination is suspected. Always use the recommended fluid type to prevent viscosity issues. If the problem persists, consult a professional or refer to the manufacturer’s troubleshooting guide for detailed steps to clear or replace clogged lines. Regular maintenance, such as filtering and replacing fluids, can help prevent future blockages. Addressing this issue promptly ensures optimal plow functionality and extends equipment lifespan.
3.2 Low Hydraulic Fluid Levels
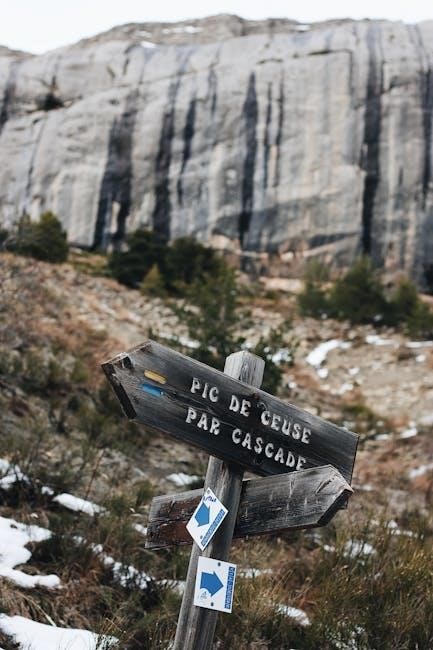
Plow Lift Mechanism Problems
Issues with the plow lift mechanism can hinder snow removal efficiency. Common causes include hydraulic malfunctions, obstructions, or worn components. Regular inspections and timely repairs are essential.
4.1 Plow Failing to Lift Properly
If your Fisher snow plow fails to lift properly, it can significantly hinder your snow removal efforts. This issue often stems from hydraulic system malfunctions, such as low fluid levels or clogged lines, which prevent the lift cylinder from functioning. Additionally, electrical faults, like blown fuses or damaged wiring, can disrupt communication between the control panel and the lift mechanism. Obstructions, such as ice or debris, may also restrict movement. It’s crucial to inspect the hydraulic lines for blockages and ensure fluid levels are adequate. Checking the electrical connections and fuses is another essential step. If the problem persists, consulting a professional or referencing the Fisher troubleshooting guide is recommended to restore proper plow functionality and maintain winter maintenance efficiency.
4.2 Plow Dropping Unexpectedly
If your Fisher snow plow drops unexpectedly, it poses a safety risk and disrupts snow removal operations. This issue may result from hydraulic system failures, such as a sudden loss of pressure or fluid leaks, which cause the lift cylinder to lose its hold. Electrical malfunctions, including faulty limit switches or wiring issues, can also trigger unintended lowering. Additionally, mechanical components like worn or damaged lift chains or springs may contribute to the plow dropping. To address this, inspect the hydraulic lines for leaks, test electrical connections, and ensure all mechanical parts are in good condition. Resetting the control panel or replacing faulty switches may resolve the issue. If the problem persists, consulting a professional or the Fisher troubleshooting guide is recommended to ensure safe and reliable operation.
Blade Angle Adjustment Issues
Blade angle adjustments are crucial for effective snow removal. Issues like improper angling or difficulty adjusting manually can hinder performance. Check for obstructions, ensure hydraulic fluid levels are adequate, and verify electrical connections to resolve these problems efficiently.
5.1 Blade Not Angling Correctly
If the blade fails to angle properly, it can significantly reduce the plow’s efficiency. This issue often stems from hydraulic or electrical malfunctions. Check for clogged hydraulic lines, which may restrict fluid flow, or low hydraulic fluid levels that prevent proper pressure. Electrical issues, such as blown fuses or faulty wiring, can disrupt the control panel’s ability to signal the blade’s angle adjustment. Additionally, inspect the angle cylinders for damage or leaks, as these can hinder movement. If manual adjustment is difficult, ensure the manual override mechanism is functioning correctly. Addressing these potential causes promptly will restore the blade’s ability to angle correctly, ensuring effective snow removal. Regular maintenance, such as cleaning connections and checking fluid levels, can help prevent these issues from arising.
5.2 Difficulty Adjusting Blade Angle Manually
Manual adjustment of the blade angle can become challenging due to mechanical issues or wear. If the blade angle is difficult to adjust, inspect for obstructions or damage to the pivot points or hinges. Ensure the angle cylinders are free from debris and functioning properly. Lubricate moving parts to reduce friction and improve mobility. Check for bent or warped components that may hinder smooth operation. If the issue persists, examine the manual adjustment mechanism for damage or misalignment. Additionally, verify that the correct tools are being used for manual adjustments, as improper tools can complicate the process. Regular lubrication of pivot points and hinges can prevent stiffness and ensure smooth manual operation. Addressing these factors will help restore ease of manual blade angle adjustment, maintaining the plow’s effectiveness in various snow-clearing scenarios.
Electrical System Troubles
Electrical issues can disrupt plow functionality. Common problems include blown fuses, faulty wiring, or corroded connections. Always check the fuse box and inspect wiring for damage or corrosion.
6.1 Blown Fuse in the System
A blown fuse in your Fisher snow plow’s electrical system can cause sudden malfunctions. Start by locating the fuse box, typically found under the hood or in the cab. Identify the specific fuse associated with the plow system using the diagram provided in your owner’s manual. If the fuse is blown, replace it with one of the same amperage rating. Turn off the plow and vehicle before replacing the fuse to ensure safety. If the fuse blows again, inspect for short circuits or overloaded components. Regularly check wiring for damage or corrosion, as these are common causes of blown fuses. Addressing the root cause is crucial to prevent recurring issues. Always consult a professional if problems persist.
6.2 Wiring Issues Causing Malfunctions
Wiring issues are a common cause of malfunctions in Fisher snow plows. Begin by inspecting the wiring harness for signs of damage, such as cuts, corrosion, or loose connections. Use a multimeter to test for continuity and voltage drops. If a wire is damaged, repair or replace it promptly. Check connections at the control panel, solenoids, and sensors, as these are prone to wear. Corrosion at connectors can disrupt communication between components, so clean or replace corroded terminals. Consult your wiring diagram to trace circuits and identify faulty sections. After repairs, test the system to ensure proper function. Addressing wiring issues early prevents further damage and ensures reliable operation of your snow plow. Always follow safety guidelines when working with electrical systems to avoid injury or additional damage.